Introduction
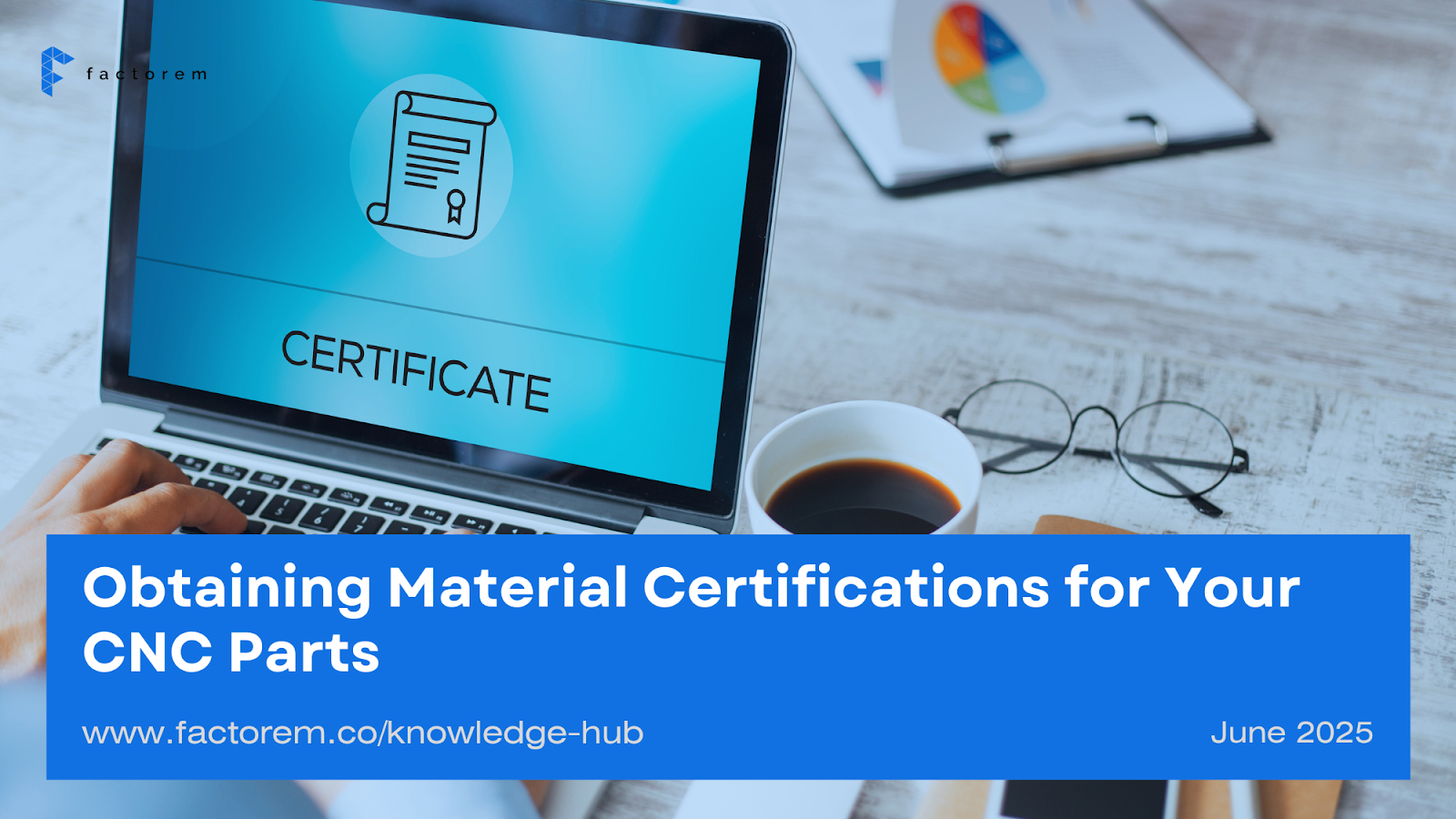
In the precision-driven world of CNC machining, the quality of your final part is only as good as the material it's made from. Ensuring that your raw materials meet exact specifications is not just a matter of good practice; it's often a regulatory and contractual necessity, especially for critical applications in industries like aerospace, medical devices, defense, and automotive. This is where material certifications become indispensable. These documents provide documented proof of a material's composition, properties, and compliance with industry standards. Without them, verifying quality, ensuring traceability, or even selling your product can be impossible, leading to costly delays, rejections, or even safety failures.
At Factorem, we understand the critical importance of material certifications for your CNC machined parts. Our process is designed to facilitate the seamless acquisition of necessary documentation, ensuring your components are built from verified materials and meet all compliance requirements. This article will explore the different types of material certifications, their importance, and how Factorem supports you in obtaining them, serving as a vital chapter in our comprehensive Ultimate Guide to CNC Machining.
Why Material Certifications are Critical
Material certifications serve several vital functions in modern manufacturing:
- Quality Assurance: They verify that the raw material used for your CNC part meets the specified chemical composition, mechanical properties (e.g., tensile strength, yield strength, hardness), and physical characteristics. This prevents the use of substandard or incorrect materials that could compromise part performance and safety.
- Traceability: Certifications provide a documented history, allowing the material to be traced back to its origin (e.g., melt number, lot number) and through the supply chain. This is crucial for isolating issues in case of a material defect or recall.
- Regulatory Compliance: Many industries operate under strict regulations that mandate material traceability and certification (e.g., FDA for medical devices, FAA for aerospace components). Without proper documentation, your parts may not be approved for use or sale.
- Customer Requirements: Customers often explicitly require specific material certifications as part of their purchase orders to ensure their own compliance and quality standards are met.
- Risk Mitigation: By verifying material quality upfront, certifications help mitigate risks of product failure, liability issues, and costly production delays or recalls.
- Enhanced Reputation: Providing comprehensive material certifications demonstrates a commitment to quality, transparency, and adherence to industry best practices, building trust with your clients.
Common Types of Material Certifications
When sourcing CNC machined parts, you will most commonly encounter the following types of material certifications:
- 1. Material Test Reports (MTRs) / Mill Certificates:
- What it is: This is the most fundamental and frequently requested material certification. Issued by the raw material manufacturer (the "mill"), it certifies the exact chemical composition and mechanical properties of a specific batch (or "heat") of material.
- What it includes: Typically details like ASTM/ASME standards compliance, specific size/shape, chemical analysis (e.g., percentages of carbon, chromium, nickel), mechanical properties (e.g., tensile strength, yield strength, elongation), heat treatment details (if applicable), and the country of melt and manufacture. The "heat number" is crucial for traceability.
- Importance: Provides direct evidence that the purchased raw material meets the specified technical requirements for your part. Essential for critical applications where material integrity is paramount.
- 2. Certificates of Conformance (CoC) / Certificates of Conformity:
- What it is: A broader document, typically issued by the manufacturer of the final part, stating that the product has been manufactured in accordance with specified requirements, drawings, standards, or purchase order details. It confirms that the product conforms to what was ordered.
- What it includes: Often references relevant standards (e.g., ISO 9001, specific industry standards), outlines the general manufacturing process, and confirms that the product meets the agreed-upon specifications. It may or may not include detailed material test data, but it often confirms the material used had the necessary MTRs.
- Importance: Provides an overall assurance of quality and compliance for the finished part, confirming that the entire production process (not just the material) met the required standards.
- 3. Industry-Specific Certifications & Standards:
- Aerospace (e.g., AS9100, NADCAP):
- AS9100: A widely adopted quality management system (QMS) standard for the aerospace industry, based on ISO 9001 with additional aerospace-specific requirements. Certification to AS9100 indicates a manufacturer's commitment to quality and compliance with aerospace standards, including stringent material control and traceability.
- NADCAP (National Aerospace and Defense Contractors Accreditation Program): Provides accreditation for specific manufacturing processes critical to aerospace, such as welding, heat treatment, non-destructive testing (NDT), and chemical processing. If your part requires these processes, ensuring the manufacturer has NADCAP accreditation for those specific processes is vital.
- Material Specifications (AMS): Aerospace Material Specifications (AMS) define the requirements for specific materials used in aerospace, such as aluminum alloys (e.g., AMS 4044, AMS 4037) and titanium alloys (e.g., AMS 4928). MTRs for these materials will reference these AMS standards.
- Medical Devices (e.g., ISO 13485, FDA UDI):
- ISO 13485: A QMS standard specifically for medical devices. It emphasizes risk management, design controls, and traceability throughout the product life cycle. Manufacturers producing medical device components must adhere to this standard.
- FDA Unique Device Identification (UDI) System: In the US, the FDA requires most medical devices to have a unique identifier (human- and machine-readable) for traceability, especially for Class II and Class III devices. Manufacturers must maintain detailed production records linked to these UDI.
- RoHS Compliance (Restriction of Hazardous Substances): Mandates the restriction of certain hazardous materials (e.g., lead, mercury, cadmium) in electrical and electronic equipment. Critical for parts intended for the EU market.
- REACH Compliance (Registration, Evaluation, Authorisation and Restriction of Chemicals): An EU regulation that addresses the production and use of chemical substances and their potential impacts on human health and the environment.
- Aerospace (e.g., AS9100, NADCAP):
Factorem's Process for Material Certifications
Factorem streamlines the process of obtaining necessary material certifications for your CNC parts, integrating it directly into our order fulfillment:
- Specification at Quoting Stage: When you upload your design files to Factorem's platform, you are prompted to specify your material requirements, including any necessary certifications (e.g., "MTR 3.1 required," "RoHS compliant material"). This ensures that certification needs are known and accounted for from the very beginning.
- Vetted Network of Certified Suppliers: Factorem's global manufacturing network includes partners who possess various industry-specific certifications (e.g., ISO 9001, AS9100, ISO 13485 capable facilities). Our system can match your project with a supplier who not only has the technical capabilities but also the necessary certifications and processes to provide the required material documentation.
- Proactive Documentation Collection: Upon order placement, Factorem works directly with the chosen manufacturer to ensure that all specified material certifications, such as MTRs, are obtained from the raw material supplier and kept on file.
- Integrated Quality Control & Verification: Our internal quality assurance process includes verification of material documentation against your specifications. This ensures that the material used for your parts matches the certified data.
- Access to Documentation: You can typically request and access copies of your material certifications directly through the Factorem platform or via our dedicated project managers. This centralized access simplifies your record-keeping and auditing processes.
- Traceability Throughout Production: Factorem's comprehensive project management system ensures material traceability is maintained throughout the CNC machining process, from raw material receipt to final part shipment. This includes tracking lot numbers and ensuring proper handling according to certified procedures.
- Support for CoC: Factorem can provide a Certificate of Conformance for your order, attesting that the manufactured parts meet your specified requirements and were produced in accordance with Factorem's quality protocols and industry best practices.
The Importance of Traceability in Action
Imagine a critical aerospace component that fails. With robust material certifications and traceability, every step can be traced:
- The part's unique identifier leads to its production batch.
- The production batch links to the specific raw material lot number.
- The raw material lot number corresponds to a specific MTR, showing its chemical composition and mechanical properties from the mill.
- This allows engineers to pinpoint whether the failure was due to a material defect, a manufacturing process error, or a design flaw, enabling rapid root cause analysis and targeted corrective actions.
Factorem's commitment to detailed documentation and process control ensures this level of traceability, providing invaluable data for quality assurance and continuous improvement.
Conclusion
Obtaining appropriate material certifications is a non-negotiable step for ensuring the quality, safety, and compliance of your CNC machined parts, especially in highly regulated industries. From fundamental Material Test Reports to overarching Certificates of Conformance and specialized industry standards, these documents provide essential proof of your material's integrity and adherence to specifications.
Factorem simplifies this complex process by integrating certification requirements into our quoting and ordering workflow. By leveraging our vetted network of certified manufacturers and providing transparent access to critical documentation, we empower you to confidently source CNC parts that meet the highest standards of quality and traceability.
Ready to ensure your CNC parts come with the right material certifications? Upload your design files to Factorem today and experience a transparent and compliant manufacturing process.
Dive into the complete CNC Machining Content Hub.