Introduction
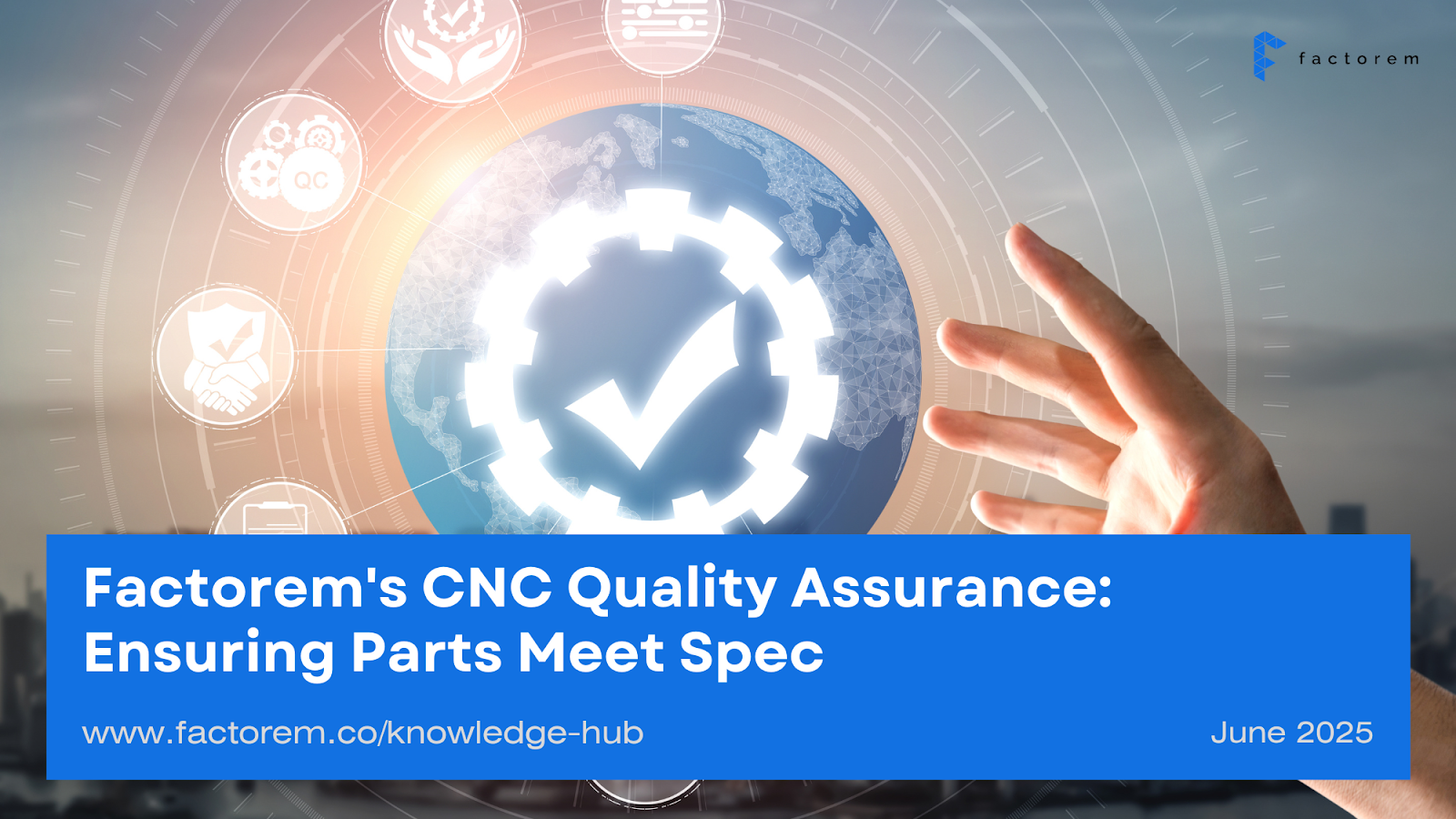
In the intricate world of CNC machining, precision is paramount. A part, no matter how complex or innovative its design, is only as valuable as its ability to perform its intended function flawlessly. This hinges entirely on quality assurance (QA) – the systematic process of ensuring that every manufactured component rigorously adheres to its specified design, dimensions, and material properties. For businesses outsourcing CNC machining, ensuring consistent quality can be a significant challenge, often leading to concerns about inconsistent results, costly reworks, and parts that simply don't "fit." Without a robust QA framework, even minor deviations can compromise product performance, trigger assembly issues, and incur substantial financial losses and reputational damage.
At Factorem, we place quality assurance at the forefront of our operations. We believe that receiving parts that precisely meet your specifications shouldn't be a gamble, but a guaranteed outcome. This article will delve into the critical importance of robust QA in CNC machining, highlight common pitfalls in quality management, and, most importantly, detail Factorem's multi-layered approach to quality assurance, designed to ensure your parts consistently meet spec, every time. It serves as a foundational chapter in our comprehensive Ultimate Guide to CNC Machining.
Why Quality Assurance is Critical in CNC Machining
The stakes for quality in CNC machining are exceptionally high, as even minor flaws can have significant repercussions:
- Functional Performance: Parts are designed to perform specific functions within an assembly. If dimensions, tolerances, or material properties are off-spec, the part may fail to function correctly, leading to product breakdown or safety hazards.
- Assembly and Fit: Inaccurate parts can cause severe assembly line disruptions, requiring manual adjustments, rework, or even scrapping entire batches, leading to increased labor costs and production delays.
- Cost of Failure: Beyond rework, poor quality can result in costly warranty claims, customer returns, product recalls, and long-term damage to a brand's reputation.
- Complexity of Modern Designs: Today's CNC parts often feature intricate geometries, tight tolerances, and specific surface finish requirements. Verifying these complex specifications requires sophisticated inspection tools and expert knowledge.
- Supplier Variability: Different manufacturers possess varying levels of equipment, expertise, and internal QA protocols. This can lead to inconsistent quality if not managed by a central, unifying system.
- Communication Gaps: Misinterpretations of technical drawings, GD&T callouts, or surface finish requirements can lead to parts being manufactured incorrectly, even with good intentions.
- Lack of Transparency: Without clear insight into a manufacturer's QA processes, clients are often left hoping for the best, rather than having confidence in the outcome.
Factorem's Multi-Layered Quality Assurance Process
Factorem's approach to quality assurance is comprehensive and proactive, addressing potential issues at every stage of the manufacturing process to ensure your parts consistently meet specifications:
- 1. Rigorous Manufacturer Vetting and Ongoing Monitoring:
- Initial Qualification: Every manufacturer in Factorem's network undergoes a stringent vetting process. This includes assessing their quality management systems (e.g., ISO 9001, AS9100 certifications), inspecting their facilities, verifying their equipment (including inspection tools like CMMs), and reviewing their track record of quality performance.
- Continuous Evaluation: Our partners are subject to ongoing performance monitoring based on client feedback, defect rates, and on-time delivery metrics. This ensures sustained adherence to our high standards.
- 2. Detailed Specification Verification and Design for Manufacturability (DFM):
- Upfront Design Review: Upon submission of your 3D CAD models and 2D technical drawings, Factorem's engineering team conducts a thorough review. We scrutinize all specified requirements, including material, dimensions, tolerances, and surface finishes.
- Proactive DFM Feedback: Crucially, we identify potential Design for Manufacturability (DFM) issues that could impact quality or cost. This could involve suggesting minor design adjustments to achieve tighter tolerances more reliably or recommending alternative manufacturing approaches that enhance part quality without compromising functionality.
- Clarification of Ambiguities: Any ambiguous specifications or potential conflicts within the drawings are flagged and clarified with you before manufacturing begins, preventing costly misinterpretations.
- 3. Standardized Quality Protocols Across the Network:
- Uniform Standards: While our network comprises diverse manufacturers, Factorem ensures a baseline of common quality checks and inspection protocols are applied. This standardizes the quality expected, regardless of which partner produces your part.
- Adherence to Industry Standards: We ensure compliance with relevant industry standards such as ISO 2768 for general tolerances, and proper application of Geometric Dimensioning and Tolerancing (GD&T) principles, as detailed in our previous articles.
- 4. Leveraging Advanced Inspection Capabilities:
- Our network includes manufacturers equipped with state-of-the-art inspection technologies essential for verifying complex CNC parts:
- CMMs (Coordinate Measuring Machines): For highly accurate 3D measurements of intricate geometries and tight tolerances.
- Optical Comparators / Vision Systems: For precise 2D measurements, profile analysis, and inspection of small, delicate features.
- Surface Roughness Testers: To objectively verify that specified surface finish requirements (e.g., Ra, Rz values) are met.
- Calibrated Gauges and Fixtures: Utilizing a range of precision tools and custom fixtures for in-process and final checks.
- Our network includes manufacturers equipped with state-of-the-art inspection technologies essential for verifying complex CNC parts:
- 5. Comprehensive Digital Traceability and Documentation:
- Full Record Keeping: All project specifications, DFM feedback, manufacturing parameters, and inspection results are digitally recorded and traceable through the Factorem platform.
- Certifications: When required, we facilitate the provision of Material Test Reports (MTRs) to verify material composition and properties, and Certificates of Conformance (CoCs), confirming that parts meet all specified requirements.
- 6. Proactive Defect Prevention Strategy:
- Our focus is on preventing quality issues from arising in the first place, rather than just identifying them after the fact. This is achieved through:
- Thorough DFM analysis and clear communication.
- Matching projects with the most capable and experienced manufacturers.
- Ensuring manufacturers have robust internal process controls.
- Our focus is on preventing quality issues from arising in the first place, rather than just identifying them after the fact. This is achieved through:
- 7. Responsive Customer Feedback Loop:
- We maintain an open channel for client feedback regarding part quality. Any reported issues are promptly investigated and directly inform the ongoing performance evaluation of our manufacturing partners, ensuring continuous improvement.
Addressing Specific Quality Needs
Factorem's QA framework is flexible enough to accommodate specialized requirements:
- Tight Tolerances and GD&T: Our expertise ensures that complex GD&T callouts are correctly interpreted and rigorously inspected.
- Material Certifications: We can facilitate the provision of specific material certifications and traceability documentation.
- Surface Finish Verification: We ensure that aesthetic and functional surface finish requirements are precisely met and verified.
- First Article Inspection (FAI): For critical components or new production runs, we support the generation and review of FAI reports, providing documented proof of conformity before full production commences.
Conclusion
Ensuring that CNC machined parts consistently meet design specifications is paramount for product success, operational efficiency, and brand reputation. The complexities of modern designs, supplier variability, and the high cost of failure underscore the critical need for a robust and transparent quality assurance system.
Factorem provides precisely this. Our multi-layered approach, encompassing rigorous manufacturer vetting, proactive DFM analysis, standardized quality protocols, leveraging advanced inspection technologies, and comprehensive digital traceability, is designed to instill confidence in every part you receive. By partnering with Factorem, you gain a commitment to precision and a system built to deliver parts that not only meet spec but exceed expectations, minimizing risks and maximizing your project's success.
Ready to experience unparalleled quality assurance in your CNC machining projects? Get an instant quote with Factorem today and ensure your parts meet spec, every time.
Dive into the complete CNC Machining Content Hub.