Introduction
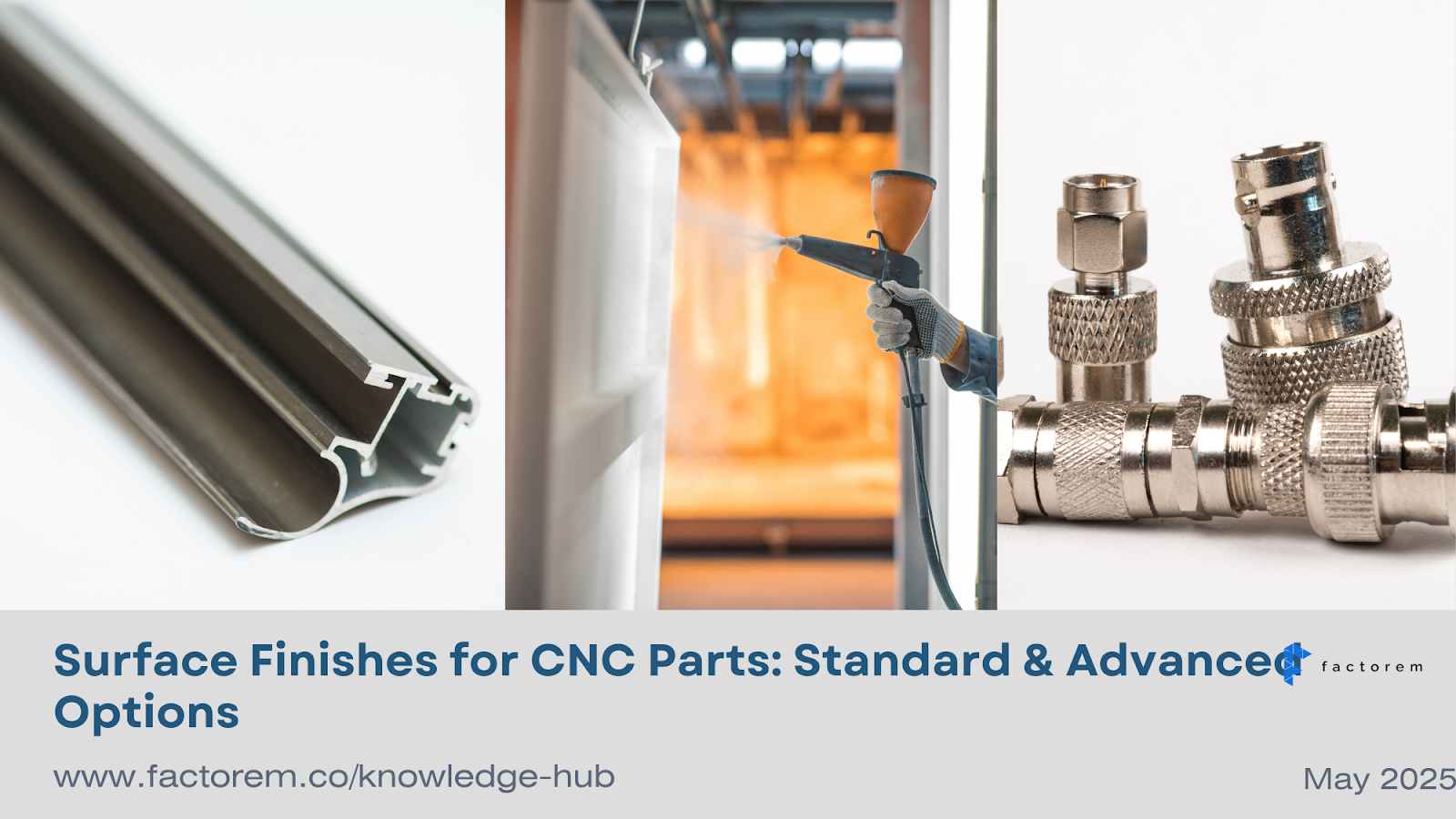
CNC machining produces parts with incredible precision and complex geometries. However, the surface left by the cutting tools, known as the "as-machined" finish, is often just the first step. Applying a surface finish is frequently necessary to enhance the part's aesthetic appeal, improve its functional performance (such as wear resistance, corrosion resistance, or electrical conductivity), or provide protection from the environment. The vast array of surface finishing options available for CNC machined parts allows for tailoring the final product to meet specific requirements across diverse industries.
This article explores the common and advanced surface finish options available for CNC machined parts. We will discuss their characteristics, typical applications, and highlight the availability of these finishes to help you choose the right treatment for your components. It serves as the foundational chapter in our comprehensive Ultimate Guide to CNC Machining.
The Baseline: As-Machined Finish
The "as-machined" surface finish is the direct result of the CNC cutting process before any additional treatments are applied. It will typically show visible tool marks, the pattern and prominence of which depend on factors like the machining strategy, tool type, cutting speed, and material.
- Characteristics: Presence of tool marks, a certain level of surface roughness (often measured in Ra - Roughness Average), and the inherent color and texture of the base material.
- Applications: Suitable for many internal features, non-cosmetic parts, or components where subsequent assembly or function is not critically dependent on a smooth surface finish. It is the most cost-effective finish as it requires no additional processing time or cost.
Standard Surface Finish Options
Beyond the as-machined state, several standard surface finishing techniques are commonly applied to CNC parts to improve their appearance or introduce basic functional enhancements.
- Deburring: This is often the first step after machining. It involves removing any burrs (small, sharp edges) left by the cutting tools using manual tools, vibratory finishing, or other methods. It's essential for safety and proper part fit.
- Bead Blasting: This process involves propelling fine glass or ceramic beads at high pressure onto the part's surface.
- Characteristics: Creates a uniform matte or satin texture, effectively removing tool marks and providing a clean, non-reflective finish. The final texture depends on the bead size and blasting pressure.
- Applications: Improves aesthetic appearance, provides a good surface for subsequent painting or coating, and can slightly increase surface hardness. Commonly used on both metal and plastic parts.
Advanced Surface Finish Options
For applications requiring enhanced durability, corrosion resistance, specific electrical properties, or a particular aesthetic, advanced surface finishing options are available. These often involve chemical or electrochemical processes, or the application of coatings.
- Anodizing (primarily for Aluminum and Titanium): This is an electrochemical process that converts the surface of the metal into a durable, porous oxide layer.
- Characteristics: Enhances corrosion and wear resistance significantly. The porous nature allows for dyeing, enabling a wide range of color options. Different types (Type I, II, and III/Hardcoat) offer varying thicknesses and hardness levels.
- Applications: Widely used in aerospace, automotive, consumer electronics, and architectural applications for both protective and decorative purposes.
- Powder Coating: This process involves electrostatically applying a dry powder made of polymer resins, pigments, and curing agents to the part, followed by curing in an oven.
- Characteristics: Creates a tough, durable, and aesthetically pleasing finish that is resistant to chipping, scratching, and fading. Available in a vast array of colors, textures (matte, satin, gloss), and finishes.
- Applications: Excellent for metal parts requiring a robust and attractive protective layer. Common in automotive, consumer goods, and industrial equipment.
- Plating (e.g., Nickel, Chrome, Zinc, Gold): This electrochemical process deposits a thin layer of a different metal onto the surface of the base material.
- Characteristics: Provides enhanced corrosion resistance, wear resistance, hardness, or electrical conductivity depending on the plating material. Can also be used for decorative purposes.
- Applications: Used across various industries for functional and aesthetic benefits, such as improving the lifespan of components in harsh environments or providing conductivity for electronic parts.
- Electropolishing (primarily for Stainless Steel): An electrochemical process that removes a thin layer of material from the surface, smoothing and brightening it.
- Characteristics: Reduces surface roughness, improves corrosion resistance, and provides a bright, passive surface.
- Applications: Common in medical, pharmaceutical, and food processing industries where hygiene and corrosion resistance are critical.
- Passivation (for Stainless Steel): A chemical treatment (typically using citric or nitric acid) that removes free iron from the surface of stainless steel, enhancing its natural corrosion resistance by promoting the formation of a protective oxide layer.
- Characteristics: Improves corrosion resistance without changing the part's appearance or dimensions.
- Applications: Essential for stainless steel parts used in corrosive environments, medical devices, and food handling equipment.
Availability of Standard and Specialized Finishes
The availability of surface finishes depends largely on the capabilities of the manufacturing partner. Most reputable CNC machining service providers offer a range of standard finishes like deburring and bead blasting as routine post-machining operations.
More advanced finishes like anodizing, powder coating, plating, electropolishing, and passivation often require specialized equipment and expertise. While some large manufacturing houses may have these capabilities in-house, it is common for CNC machine shops to work with trusted third-party specialists for these treatments. When requesting a quote, it is important to clearly specify the desired surface finish, including any relevant standards or specifications (e.g., anodizing type and color, plating material and thickness).
Choosing the Right Surface Finish
Selecting the appropriate surface finish involves considering several factors:
- Functional Requirements: Does the part need enhanced wear resistance, corrosion resistance, electrical conductivity, or other specific properties?
- Environmental Exposure: Will the part be exposed to moisture, chemicals, UV light, or extreme temperatures?
- Aesthetics: Is a specific appearance required (color, texture, gloss level)?
- Material Compatibility: Not all finishes are suitable for all materials. Anodizing, for example, is primarily for aluminum and titanium.
- Cost: Advanced finishes add cost to the part, sometimes significantly. The complexity of the part and the required surface preparation also influence the finishing cost.
- Tolerance Impact: Some finishes, like plating and thick powder coatings, add material thickness, which can affect the part's dimensions and require accounting for in the design or machining process.
Conclusion
The surface finish of a CNC machined part is more than just cosmetic; it plays a vital role in the part's performance, durability, and suitability for its intended application. From the basic as-machined surface to a wide array of standard and advanced options like bead blasting, anodizing, powder coating, and plating, understanding the characteristics and benefits of each finish is key to making informed decisions. Choosing the right surface finish can significantly enhance the value and functionality of your CNC machined components.
Navigating the diverse landscape of surface finishes and ensuring access to the specific treatments your parts require can be complex. This is where an on-demand manufacturing platform like Factorem becomes invaluable. Factorem connects you with a network of experienced manufacturers who offer a comprehensive range of standard and specialized surface finishing options for various materials. By leveraging Factorem's platform, you can easily specify the desired finish for your CNC machined parts and be confident that it will be applied by skilled professionals with the necessary capabilities, simplifying your supply chain and ensuring high-quality results.
Ready to give your CNC machined parts the perfect finish? Partner with Factorem to access a wide network of manufacturers offering diverse surface finishing capabilities. Get an instant quote today and enhance the performance and appearance of your components.
Dive into the complete CNC Machining Content Hub.