Introduction
Computer Numerical Control (CNC) machining has revolutionized manufacturing since the early 1900s. What once required skilled labor to operate individual machines like lathes, drill presses, and milling machines can now be accomplished with a single computer-programmable CNC machine. In CNC manufacturing, machines are operated via numerical control (NC), where pre-programmed computer software dictates the movement of factory tools and machinery. This automation has led to a rapid increase in the popularity of CNC machining, with many enterprises switching to automated workflows and driving the demand for custom-made machined parts.
While CNC machining offers incredible precision and efficiency, especially for custom parts, it also introduces a unique set of cost considerations that are often overlooked until they become apparent during the production process. This article aims to provide a transparent breakdown of the key factors that influence CNC machining costs, helping you make informed decisions before approaching machine shops with your unique ideas. It serves as the foundational chapter in our comprehensive Ultimate Guide to CNC Machining.
Before that, do check out our previous articles on CNC manufacturing listed below for a better understanding of the guidelines when designing parts for CNC machining.
Factorem’s ISO 2768 Machining Guidelines
Drafting technical drawings for CNC Fabrication
Dowel Pin Tolerance and Fit Standards
CNC Machining — Do you need 3/4/5 axis machining?
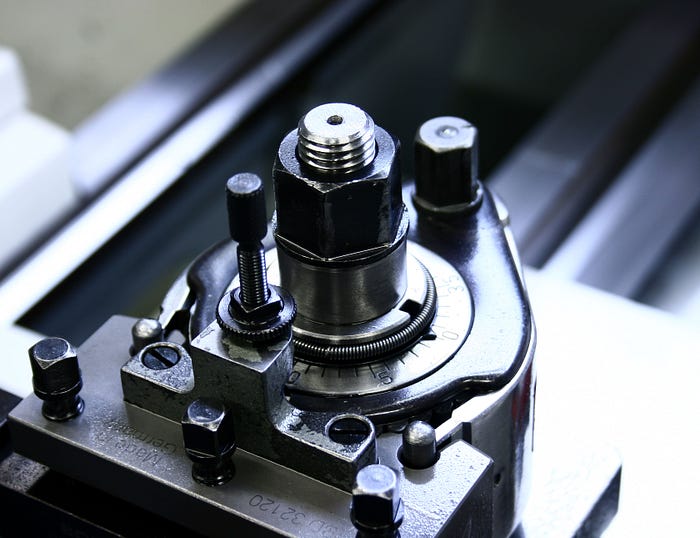
1. Higher Set-up Costs for Low-Volume Orders
One of the most significant factors contributing to the cost of custom CNC machined parts, particularly for low-volume orders (typically less than 10 pieces), is the initial set-up cost. Machine shops have fixed rates not only for powering on their machines but also for each set-up required in the machining process.
Let's illustrate this with an example:
Imagine a single part that requires machining on two separate faces. On a standard 3-axis CNC machine (the most common variant available), this would necessitate two separate set-ups. Assuming each set-up costs $40 and the machine switch-on cost is $40, the total set-up cost for a single part would amount to $120.
Now, consider if the same part needs to be produced in a quantity of 10. The total cost for the two set-ups and machine switch-on remains $120 because all 10 blocks can be loaded in the same fixture for the initial part. Even if a handling fee of $10 is applied to each of the 10 parts, the total set-up cost would be $220, which breaks down to just $22 per piece.
(None of the prices in the example above are representative of market rates and are purely for explanation purposes.)
This example clearly shows that if only a single part is made, the set-up cost per piece is almost six times more expensive compared to a larger order of 10 such parts.
Lesson: Custom parts will inherently be more expensive per unit due to these initial fixed costs. It's not uncommon for prices for orders under 10 pieces to be more than double what you might anticipate based on past experiences with bulk orders.
2. Rising Material Prices and Volatility
The global landscape, significantly impacted by events like Covid-19, has had a profound effect on the machining world. Material prices have become increasingly volatile, sometimes changing twice a week and rarely decreasing. Raw material cost is one of, if not the most, important criteria for a quotation. This means that quotations are valid for a much shorter period.
Furthermore, material stock often takes much longer to arrive due to backlogs, leading to a constantly fluctuating base price for the same part.
Lesson: Many companies and government organizations require multiple quotations for comparison. However, the decision needs to be made quickly. Hesitation can literally cost you, as material prices may increase before an order is placed.
3. Standard Raw Material Sizes and Availability
Building on the issue of rising material prices, raw materials are mass-produced in certain standard dimensions. Supply chain shortages, exacerbated by the pandemic, coupled with steep prices, mean that your trusted supplier may no longer have the exact standard metal tubes or sheets you require in stock.
Suppliers are also likely to prioritize larger orders to minimize waste and offer the best prices. They may even be unwilling to purchase specific stock material for your low-quantity request if their available material cannot suit your needs.
For example, if a machinist needs to purchase a steel tube that they don't typically keep in stock, your one-piece requirement (which might be less than a quarter of the stock tube length) doesn't make economical sense for them to take on the order. It would also be very expensive for you, as you would have to bear the cost of the entire stock tube, with no guarantee that the unused material will ever be utilized for another customer or order.
Lesson: There are a few ways to navigate material-related cost issues. The easiest is to provide the stock material yourself. This saves your supplier on material costs and increases your chances of having your order accepted, as the unused material is no longer their liability. Another option is to remain flexible with your part design, being open to changes in certain dimensions and material thickness so that the supplier can make your part from material they already have on hand.
Conclusion
Custom CNC machining offers incredible flexibility for creating unique, one-off parts, but it also brings challenges that are often overlooked. From higher setup costs to unpredictable material availability and rising prices, understanding these factors upfront can help you make smarter, faster, and more cost-effective decisions.
While the global supply chain continues to evolve, working with an experienced manufacturing partner can help you navigate these complexities with ease. That’s where Factorem comes in. By leveraging a vast network of trusted manufacturers and material suppliers, Factorem simplifies the process of sourcing, quoting, and producing custom CNC machined parts even in today’s uncertain manufacturing landscape.
Ready to turn your custom part ideas into reality? Get an instant quote with Factorem and experience a seamless, transparent process from design to delivery.
Explore the full CNC Machining Content Hub for more resources and expert insights.