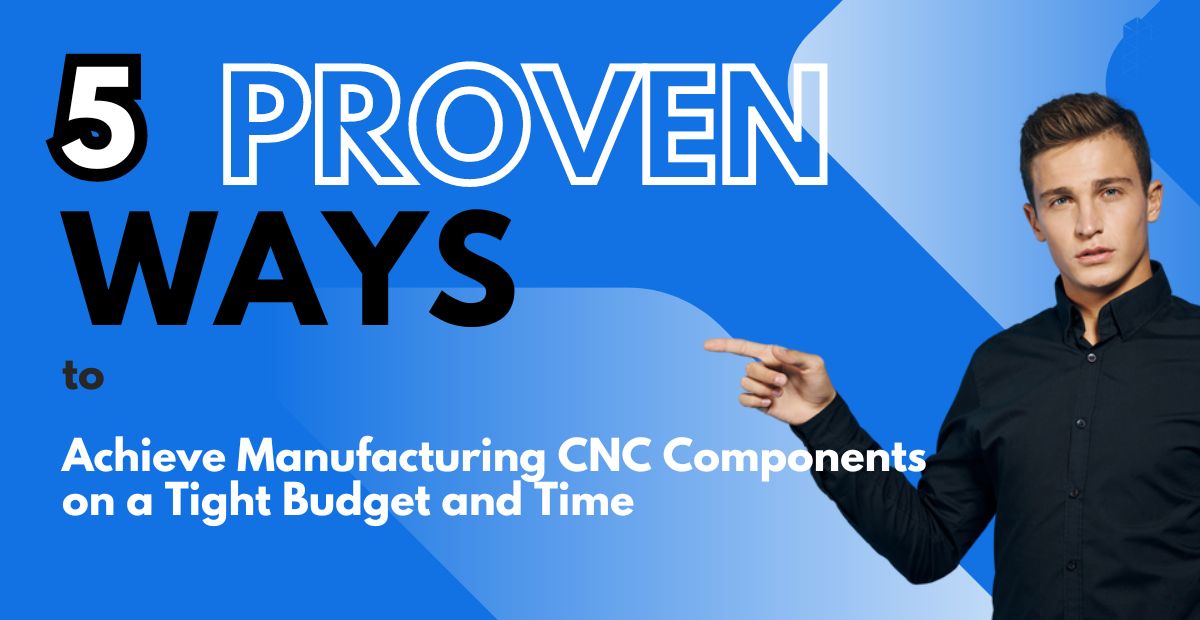
Are you feeling rushed because you have to manage the last-minute project that you need to get your CNC components manufactured within a certain budget and timeframe? Don’t worry! You have come to the right place at the right time. Here are 5 proven ways to manufacture CNC components without going over your budget and time constraints!
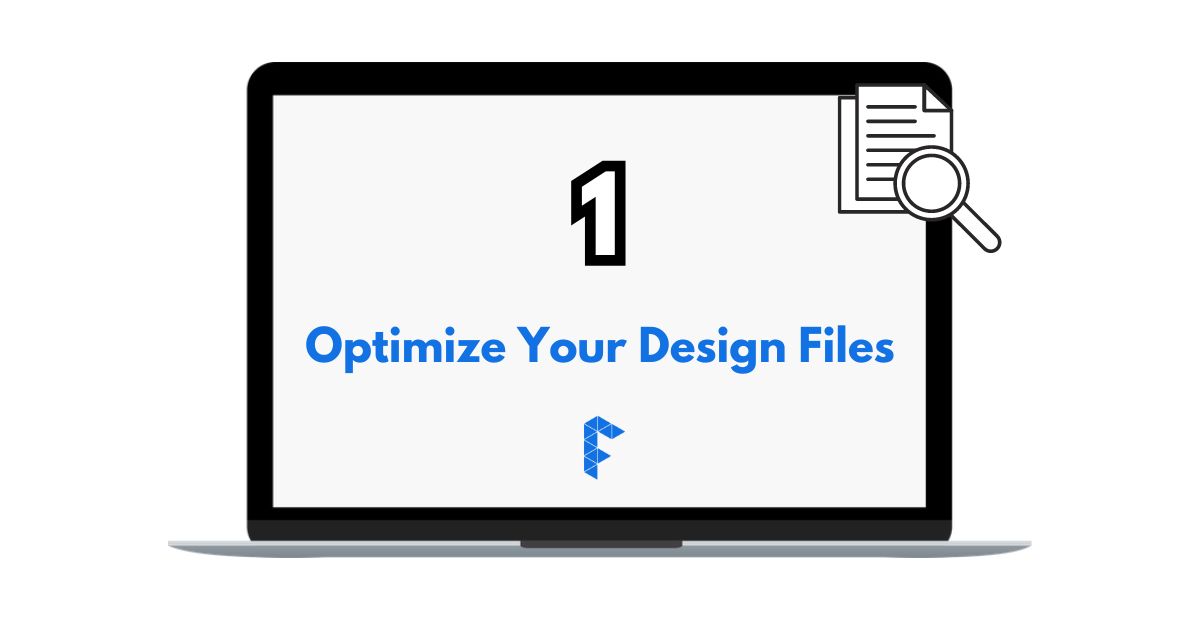
1. Optimize Your Design Files: You can start by looking at your design files again to see if your component designs are fit for manufacturability. Analyze and see if including multiple smaller holes is as effective as replacing them with one well-placed hole in terms of functionality. If you are focusing on manufacturing to meet your target cost and lead time, eliminating unnecessary parts can definitely solve the problem and help you reach your goal. If you’d like more guidelines on how to draft the technical drawing for the CNC machining, details are explained here.
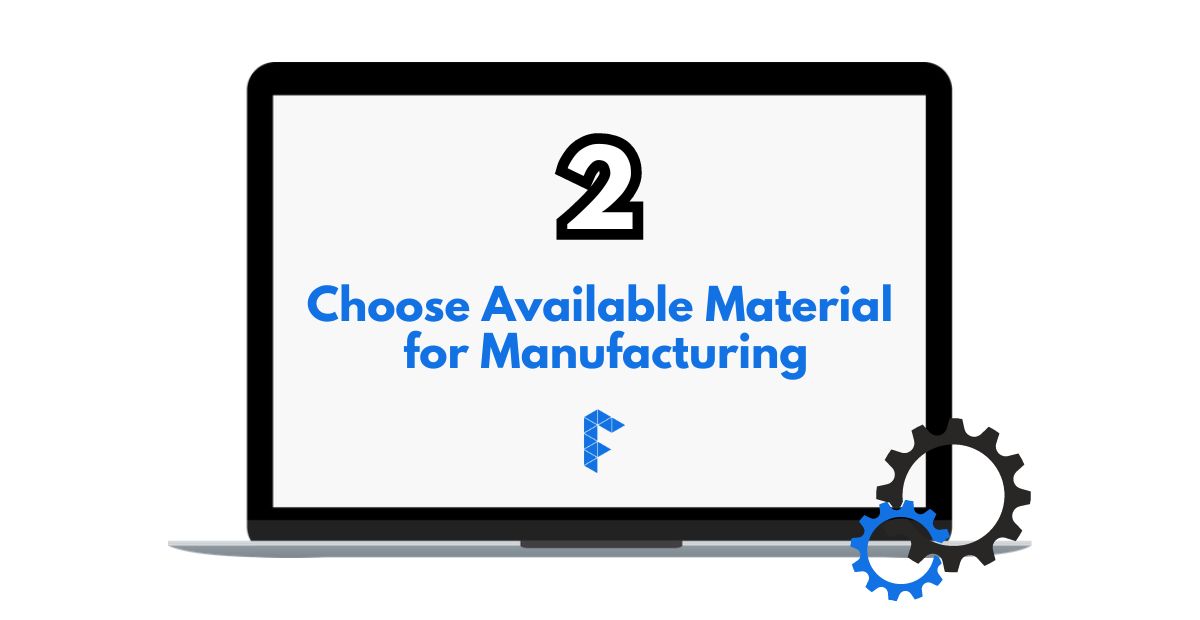
2. Choose Available Material for Manufacturing: The most common materials used for manufacturing CNC components are steel, aluminum, titanium, brass, copper, stainless steel, and plastic. While choosing the material, instead of going for custom material, consider using the available material that meets your component requirements. In this way, you can cut down on the time spent searching for the custom material, which leads to cost- savings.
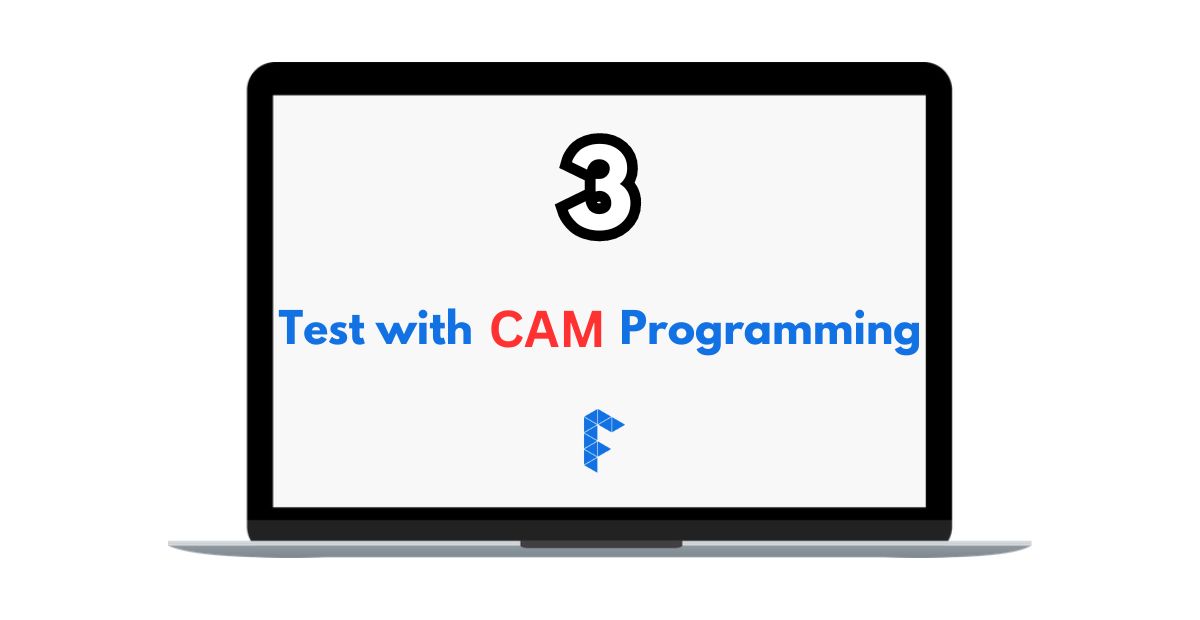
3. Test with CAM Programming: If you are a manufacturer who just has the design file and no technician to go through the following process, you can skip to Step 5.
CAM stands for computer-aided manufacturing, and it is used to develop a wide range of CNC equipment, including CNC milling machines, CNC turning machines, and machines for cutting-edge machining and additive manufacturing. A qualified CAM programmer can optimize and minimize the toolpaths, which will notably decrease the machining lead time. Using the software can identify possible issues that can occur when actual manufacturing takes place. We can reduce time and cost in advance by eliminating them.
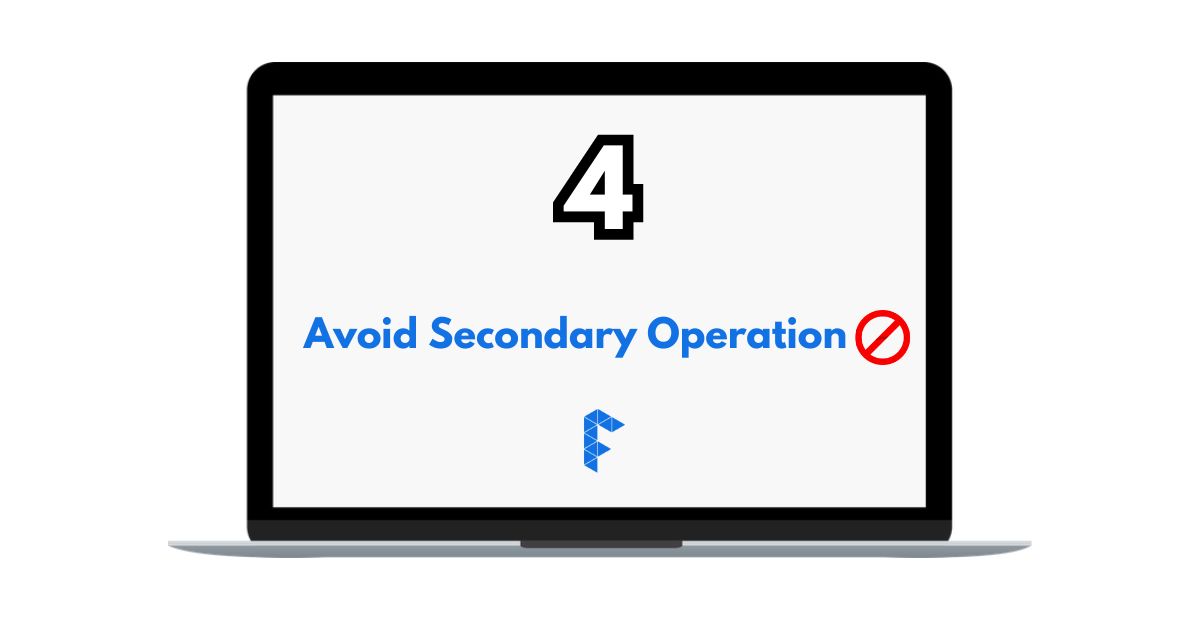
4. Avoid Secondary Operation: Check to see if your component surface requires a mirror finish. Surface finishing comes in a variety of textures, ranging from satin and glossy to more complicated ones like leather and fabric. Choosing a more flexible surface finish can give you more ease in manufacturing. Second thing to examine is that threading or tapping functions can be included into the program to avoid additional separate operations. Checking these before the actual manufacturing can definitely reduce the cost and lead time in meeting your target.
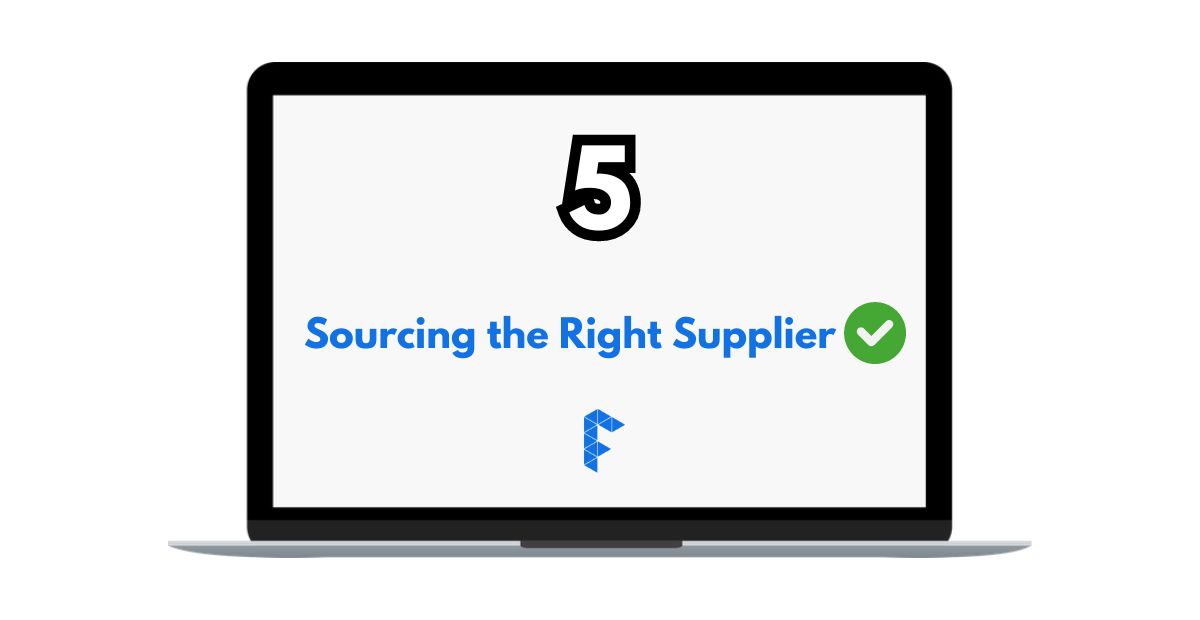
5. Sourcing the Right Supplier: Try to explore different options by keeping your supplier range wide and compact, not only locally but also internationally. By having them all on your radar, you have plenty of options in your hands to choose from. Since you already have your target manufacturing cost and lead time planned ahead, request multiple quotations from them by explaining your requirements to them. You can filter out each supplier depending on their quotation response time and whether they can meet your standard needs for your project.
However, if you do not have the relaxation to research and reach out to the suppliers, Factorem has a variety of verified suppliers from all around the world in their cycle.
We find the best manufacturing solution for your component design, target price, and lead time needs through our AI-driven order matching system.
All you need to do is upload the design file, type in your target price and lead time, and the quotation will appear. They will do all the magic to get your CNC components delivered to your doorstep on your expected date.