CNC Machining Fundamentals: Core Concepts & Benefits Explained
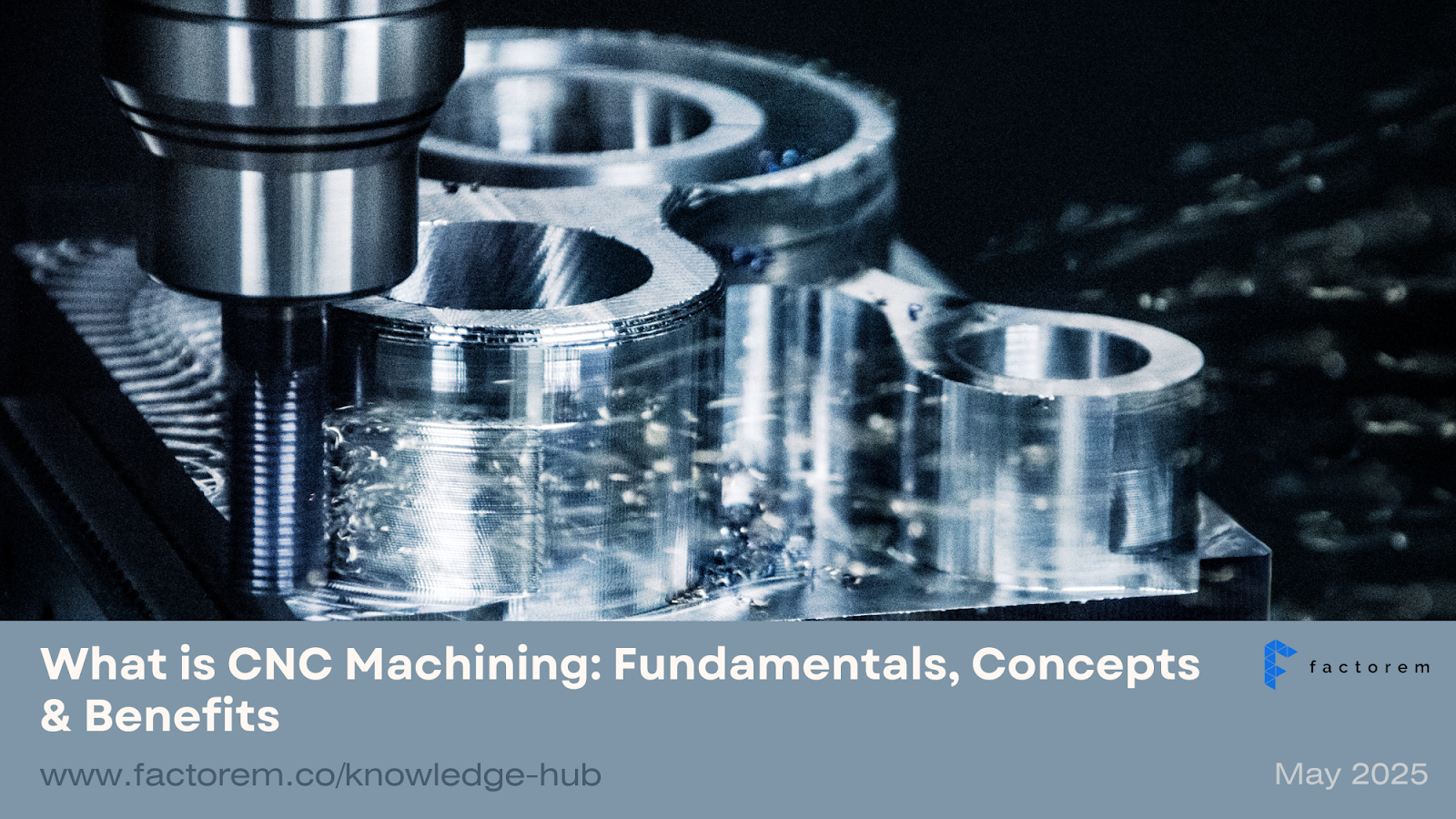
Computer Numerical Control (CNC) machining is a cornerstone of modern manufacturing, enabling the creation of precise and complex parts from a wide range of materials. Whether you're a Startup Engineer developing your first physical prototype, a Procurement Manager sourcing reliable production partners, or an R&D Lead exploring intricate designs, understanding the fundamentals of CNC is essential.
This article breaks down the core principles of CNC machining, explains how the process works, introduces key terminology, and highlights the significant benefits it offers. It serves as the foundational chapter in our comprehensive Ultimate Guide to CNC Machining.
Defining CNC Machining: Precision Through Subtraction
At its heart, CNC machining is a subtractive manufacturing process. Unlike additive manufacturing (3D printing) which builds parts layer by layer, subtractive processes start with a solid block of material (called a workpiece or blank) and selectively remove material using computer-controlled cutting tools to achieve the desired shape.
The "CNC" stands for Computer Numerical Control. This means that pre-programmed computer software dictates the movement of factory tools and machinery. Instead of manual operation, CNC systems automate the control of tools like mills, lathes, routers, and grinders, following coded instructions to cut and shape the workpiece with incredible accuracy.
The Basic CNC Machining Process: From Digital Design to Physical Part
While the specifics vary by machine and complexity, the fundamental workflow generally involves these steps:
- CAD Model Creation: Designers create a 2D or 3D model of the part using Computer-Aided Design (CAD) software. (See our guide on Preparing Design Files for CNC)
- CAM Toolpath Generation: Computer-Aided Manufacturing (CAM) software translates the CAD model into machine code (typically G-code) that dictates tool movements, speeds, and feeds. This process generates the toolpaths the machine will follow.
- Machine Setup: A skilled operator secures the workpiece onto the CNC machine table and loads the necessary cutting tools into the machine's spindle or turret.
- Machining Execution: The operator initiates the program. The CNC machine precisely executes the G-code instructions, moving the cutting tools and/or the workpiece to remove material and shape the final part.
Core Concepts & Terminology You Need to Know
Understanding these basic terms will help you navigate discussions about CNC machining:
- Milling: A process using rotating multi-point cutting tools to remove material from the workpiece. Used for creating flat surfaces, slots, pockets, and complex contours.
- Turning: Typically performed on a lathe, this involves rotating the workpiece against a stationary single-point cutting tool. Used primarily for creating cylindrical or conical shapes (e.g., shafts, pins).
- Axes: Refers to the directions of movement controlled by the CNC machine.
- 3-Axis: Moves the tool (or workpiece) along the X, Y, and Z linear axes. Suitable for simpler geometries.
- 4-Axis & 5-Axis: Add rotational axes, allowing the tool to approach the workpiece from more angles, enabling the creation of much more complex shapes in fewer setups. (Learn more: 3-Axis vs 5-Axis CNC Explained)
- G-code: The most common programming language used to tell CNC machines how and where to move, controlling speeds, feeds, coolant, and tool changes.
Key Benefits of CNC Machining
Why choose CNC machining? It offers several compelling advantages:
- High Precision & Accuracy: Computer control allows for extremely tight tolerances (the permissible limit of variation in a physical dimension) and high dimensional accuracy, critical for functional parts. (See our guide on Mastering Tolerances in CNC)
- Excellent Repeatability & Consistency: Once programmed, a CNC machine can produce identical parts repeatedly, ensuring consistency across production runs – a key benefit for Procurement Managers seeking reliable quality.
- Material Versatility: CNC machines can effectively shape a vast range of engineering materials, including various metals (Aluminum, Steel, Titanium, Brass) and rigid plastics (ABS, Polycarbonate, Nylon, PEEK, Delrin). This offers designers significant flexibility. (Explore options in our CNC Materials Guide)
- Scalability: The process is suitable for one-off prototypes (Startup Engineers), low-to-mid volume production runs, and even high-volume manufacturing with optimized setups. (Learn about Scaling with Factorem)
- Efficiency for Certain Geometries: While complex freeform shapes might favor 3D printing, CNC is often highly efficient for parts with prismatic shapes, holes, threads, and precise mating surfaces.
Conclusion: The Foundation of Precision Manufacturing
CNC machining is a powerful and versatile subtractive manufacturing process fundamental to creating high-precision components from a wide array of materials. Its ability to deliver accuracy, repeatability, and scalability makes it indispensable for prototyping, tooling, and production across diverse industries.
Understanding these core concepts provides a solid foundation as you delve deeper into specific materials, design considerations, and sourcing options.
Ready to learn more or start your CNC project?
- Continue exploring our Ultimate Guide to CNC Machining for detailed insights.
- Discover Factorem's CNC Machining Services.
- Request Your CNC Quote Today ->