Introduction
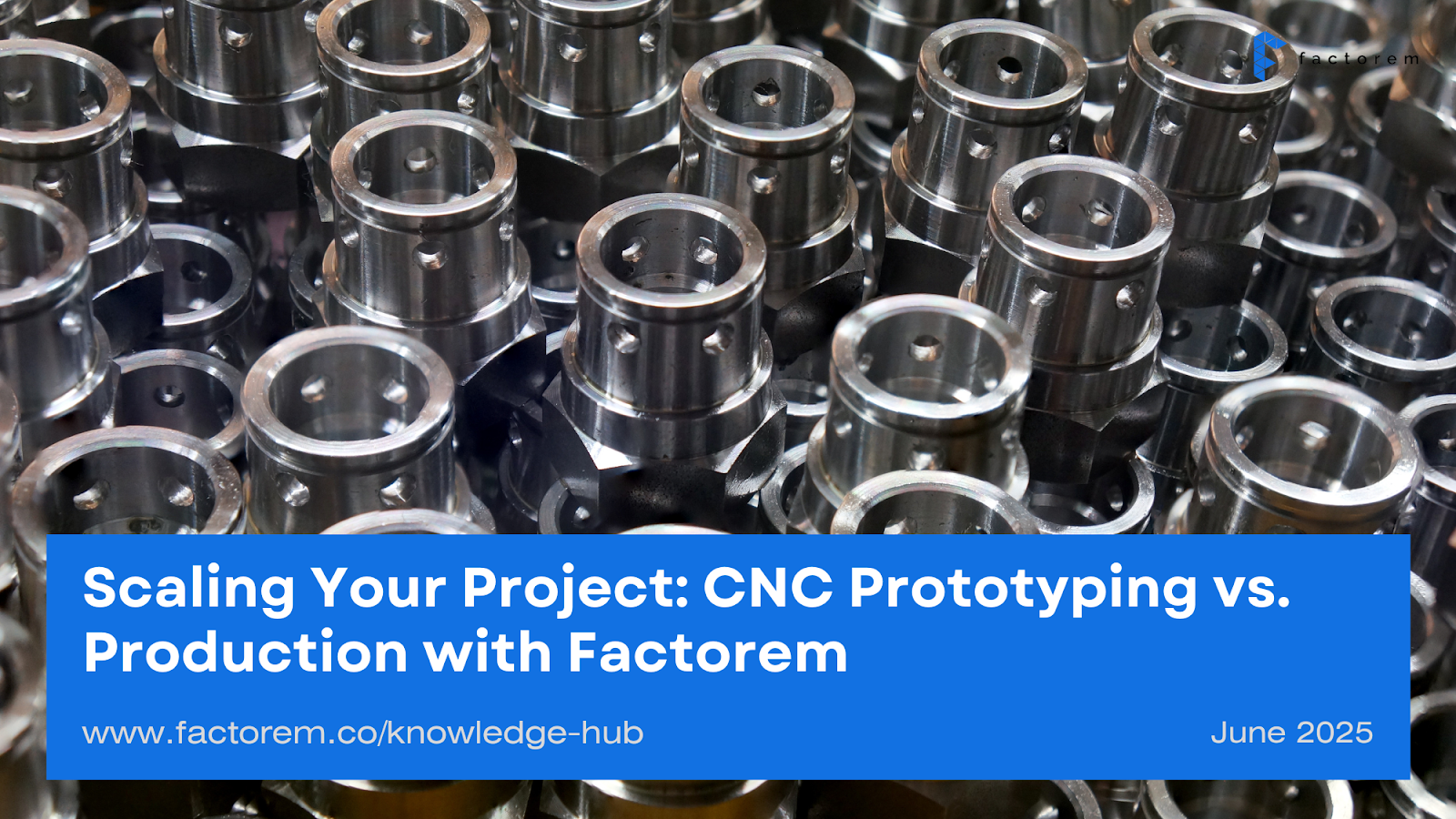
Bringing a new product to market is an exciting journey, but it often involves a critical transition: moving from initial concept and prototyping to full-scale production. For CNC machined parts, this transition is particularly nuanced. What works efficiently and cost-effectively for a single prototype or a small batch may become prohibitively expensive or unmanageable at high volumes. Businesses frequently struggle with understanding these inherent differences, leading to unexpected costs, quality inconsistencies, and delays when attempting to scale their projects.
At Factorem, we recognize that effective scaling is key to successful product launches. Our platform and expertise are designed to bridge the gap between prototyping and mass production, offering a seamless and optimized pathway for your CNC machining needs, regardless of volume. This article will explore the distinct characteristics of CNC prototyping versus production, highlight the common challenges in scaling, and crucially, demonstrate how partnering with Factorem provides the clarity, consistency, and efficiency required to scale your project with confidence. It serves as a foundational chapter in our comprehensive Ultimate Guide to CNC Machining.
Understanding CNC Prototyping vs. Production
While both prototyping and production utilize CNC machining, their goals, methodologies, and cost structures differ significantly:
- CNC Prototyping (Low Volume):
- Goal: To test, validate, and iterate on a design's form, fit, and function. The focus is on rapid iteration and design flexibility.
- Volume: Typically very low (1 to 10 pieces).
- Cost per Unit: Inherently higher due to fixed setup costs (programming, tooling setup, initial machine calibration) being amortized over a small number of parts.
- Tooling: Often uses standard, general-purpose tooling. Dedicated custom fixtures are rare or very simple, as design changes are expected.
- Lead Time: Prioritizes speed for quick design validation and multiple iterations.
- Material: May use less expensive, easily machinable materials for initial tests, not necessarily the final production material.
- CNC Production (Medium to High Volume):
- Goal: To manufacture large quantities of identical parts consistently, cost-effectively, and efficiently. The focus is on repeatability and optimization.
- Volume: Ranges from medium (100s) to high (10,000s+).
- Cost per Unit: Significantly lower due to economies of scale. Fixed setup costs are spread across many parts, and bulk material purchasing reduces raw material costs.
- Tooling: Often involves investing in optimized, dedicated fixtures and custom tooling to maximize efficiency, reduce cycle times, and ensure repeatability.
- Lead Time: Optimizes for efficient batch processing and reliable delivery schedules.
- Material: Uses the precise final production material, often sourced in bulk for cost savings.
Common Challenges When Scaling Your Project
The transition from prototyping to production is fraught with potential pitfalls if not managed correctly:
- Design for Manufacturability (DFM) Issues: A prototype design, while functional, might not be optimized for mass production. Complex features, tight tolerances, or material choices can become cost-prohibitive or create production bottlenecks at scale.
- Cost Escalation: Without proper planning, per-unit costs can unexpectedly skyrocket in production if prototyping-era assumptions are carried over, or if DFM is not considered.
- Supplier Incompatibility: Prototyping shops often aren't equipped for high-volume production, forcing a switch to a new supplier, which introduces new vetting, communication, and quality risks.
- Maintaining Quality Consistency: Ensuring that thousands of parts consistently meet the same quality standards as a handful of prototypes requires robust quality control systems that many smaller shops lack.
- Lead Time Management: Managing larger production runs involves complex logistics, material procurement, and scheduling, which can lead to significant delays if not expertly handled.
- Material Sourcing: Sourcing materials in production volumes at competitive prices, while maintaining quality and traceability, is a different challenge than buying small quantities for prototypes.
Factorem's Role in Seamlessly Scaling Your Project
Factorem's platform and integrated service model are specifically designed to address the complexities of scaling, ensuring a smooth transition from prototype to full production:
- 1. Unified Platform for All Volumes:
- Single Partner: Eliminate the need to switch suppliers as your project scales. Factorem can manage your orders from a single prototype to thousands of production units through our diverse network.
- Consistent Communication: All your project details, design iterations, and communications are centralized on one platform, ensuring continuity regardless of volume.
- 2. Proactive Design for Manufacturability (DFM) Feedback:
- Early Optimization: Our engineering team provides DFM analysis during the quoting process, identifying potential manufacturing challenges and cost drivers before production begins, whether for a prototype or a production run.
- Cost-Efficient Scaling: We help you optimize designs to be both functional for prototyping and cost-effective for mass production, preventing expensive redesigns later.
- 3. Optimized Costing Across All Stages:
- Transparent Breakdowns: Our quoting system provides clear cost breakdowns for different volumes, highlighting how per-unit costs decrease with increased quantity due to economies of scale. Read details about how we ensure accurate and upfront quotes.
- Volume-Based Savings: We leverage our network's bulk material purchasing power and optimized production processes to offer competitive pricing at every stage of your project's growth.
- 4. Dynamically Matched Vetted Manufacturer Network:
- Right Manufacturer for the Job: Our intelligent system matches your project not just by capability, but by optimal volume. We have partners specializing in rapid prototyping and others excelling in high-volume, cost-optimized production.
- Diverse Capabilities: Access a wide range of machines, materials, and post-processing capabilities suitable for both early-stage development and full-scale manufacturing.
- 5. Unwavering Quality Consistency:
- Standardized Protocols: Factorem enforces rigorous, standardized quality control procedures across our entire network, ensuring that the precision and consistency achieved in your prototypes are maintained through every production run.
- Traceability: We ensure robust traceability for materials and production processes, critical for managing quality in high-volume manufacturing.
- 6. Centralized Project Management and Logistics:
- Simplified Oversight: Factorem handles all aspects of project management, from order placement and production scheduling to quality checks and logistics, regardless of the volume.
- Reliable Delivery: Our established network and processes ensure more predictable lead times and reliable delivery, minimizing supply chain disruptions as you scale.
Addressing Specific Scaling Needs
Factorem goes beyond simply handling different volumes to cater to the unique requirements of scaling:
- Iterative Prototyping Support: Facilitate rapid turns for multiple design iterations, crucial for complex product development before committing to production.
- Production Planning Assistance: Our team can provide guidance on optimal batch sizes, material procurement strategies, and scheduling for efficient large-scale manufacturing.
- Material Transition Management: Help navigate the transition from prototype-friendly materials to final production-grade materials, considering cost and performance.
- Post-Processing Consistency: Ensure that surface finishes, heat treatments, and other post-machining processes are applied consistently and cost-effectively across all production volumes.
Conclusion
Successfully scaling your CNC machining project from prototyping to full production is a complex endeavor that demands careful planning, expertise, and the right manufacturing partner. The distinct requirements and challenges of each stage from higher per-unit costs and flexibility in prototyping to lower per-unit costs and consistency in production underscore the need for a unified and intelligent approach.
Factorem simplifies this critical transition by offering a seamless, integrated solution that supports your project at every volume. By providing proactive DFM feedback, transparent and optimized costing, access to a dynamically matched network of vetted manufacturers, and consistent quality assurance, we enable you to scale your innovations with confidence. Partner with Factorem to eliminate the typical headaches of scaling and ensure your product reaches the market efficiently and cost-effectively.
Ready to confidently scale your CNC machining projects? Get an instant quote with Factorem today and experience a seamless transition from prototype to production.
Dive into the complete CNC Machining Content Hub.